Worldwide Leader In Preheater
WEBBER INTERNATIONAL is one of the technical leaders worldwide in this field. The raw meal processed in the kiln first passes through the preheater absorbing the heat content of the kiln and gases minimizing the heat consumption of the system. WEBBER INTERNATIONAL Preheaters with modern-designed cyclones produce low-pressure drops and are high in separation efficiency. The resulting low waste gas temperatures lead to reduced heat losses, waste gas quantities, CO2 emissions, dust emissions and electrical energy consumption.
Technical characteristics of nano wear-resistant sinter cast inner cylinder of preheaters
High-temperature resistance: Since the nano-sinter-cast inner cylinder is made of SiC and WB2O3 as the main raw materials and is manufactured by recrystallizing at a high temperature of 2000°C, it can withstand a temperature as high as 1500°C.
High wear resistance and sound erosion resistance: Being made of SiC and WB2O3, sinter casts have a Moh’s hardness equal to or larger than 9, making them highly resistant to wearing and erosion.
Corrosion resistance: sinter casts have superior corrosion resistance properties since the high-temperature performance of SiC and WB2O3 is stable and does not react with any complex gas and acid-base components at high temperatures.
Anti-skinning and non-adhesion: SiC and WB2O3 are stable in terms of high-temperature chemical properties. They do not react with cement raw materials or acid and alkali components and are therefore free from adhesion or skinning.
Good thermal shock performance: Due to nano-SiC and WB2O3 sinter casts have good thermal conductivity, small thermal expansion coefficient, good thermal resistance, and resistance to sudden changes of cold and hot can reach more than 50 times.
Lightweight and convenient installation: With the reasonable modular connection design, the product features easy installation and a weight of only one-third that of the heat-resistant steel Ni20Cr25 inner cylinders, making it able to reduce labour intensity, reduce downtime, and improve production efficiency.
Highlights of the new low pressure cyclones are
- 270° inlet spiral with improved inlet geometry
- An optimum of separation efficiency and pressure drop is obtained by properly dimensioned immersion tube, separation efficiency of top stage approx. 95%
- Steep cones to minimize coating tendency
- Low gas flow velocities in the immersion tubes between 10 and 15 m/s
ADVANTAGES
- High-temperature resistance
- Wear resistance
- Corrosion resistance
- Anti skinning
- Lightweight
- Sound thermal shock stability
- Reasonable structure and optimized modular hanging
- Easy to install
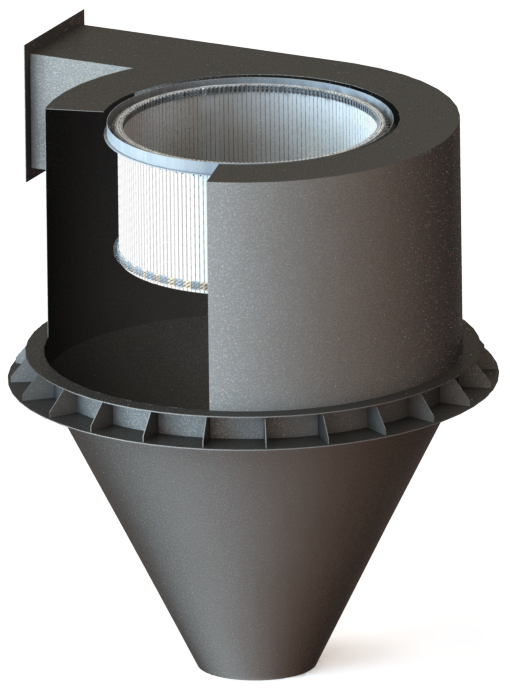